In the fast-paced world of industrial automation, Programmable Logic Controllers (PLCs) play a crucial role in enhancing efficiency, productivity, and control. Let’s dive into the fundamental questions surrounding PLCs to understand their significance and applications.
What is PLC in simple words?
In simple terms, a Programmable Logic Controller (PLC) is a specialized computer used in industries to control and automate various manufacturing processes. It operates by reading input signals, processing them with a programmable logic program, and triggering output signals to control machinery or processes.
What is a PLC and HMI?
PLC and Human-Machine Interface (HMI) often work hand in hand. While a PLC manages the logic and control of processes, an HMI provides a user-friendly interface for monitoring and interacting with the system. Together, they form a powerful combination for seamless industrial automation.
What is PLC programming?
PLC programming involves creating a set of instructions that the PLC follows to control different processes. This programming is typically done using ladder logic, a graphical programming language resembling relay logic diagrams. Skilled programmers input commands to manage the behavior of the PLC.
What is PLC basics?
PLC basics encompass understanding the key components, such as the processor, input, and output modules, and communication interfaces. It also involves grasping the programming languages, common instructions, and the overall functioning of the PLC within an industrial setting.
What are some popular PLC brands in the industry?
When it comes to Programmable Logic Controllers (PLCs), several reputable brands have made a mark in the industrial automation landscape. Here’s a list of some prominent PLC brands:
- Siemens: Siemens is a global leader in industrial automation, known for its powerful and reliable PLCs. Their SIMATIC series is widely used across various industries.
- Allen-Bradley (Rockwell Automation): Allen-Bradley, a brand under Rockwell Automation, offers a comprehensive range of PLCs. The ControlLogix and CompactLogix series are particularly popular.
- Schneider Electric: Schneider Electric’s Modicon PLCs are well-regarded for their versatility and scalability. They cater to diverse industrial applications.
- Mitsubishi Electric: Mitsubishi PLCs, part of the MELSEC series, are recognized for their precision and performance. They are commonly employed in manufacturing processes.
- ABB: ABB provides PLC solutions that integrate seamlessly with their automation offerings. The AC500 series is a notable choice for various automation tasks.
- Omron: Omron PLCs, such as the CP1E and CP1H series, are known for their user-friendly programming interfaces and reliability in control applications.
- Delta Electronics: Delta PLCs are widely used for their cost-effectiveness and efficiency. The DVP series caters to a broad spectrum of automation needs.
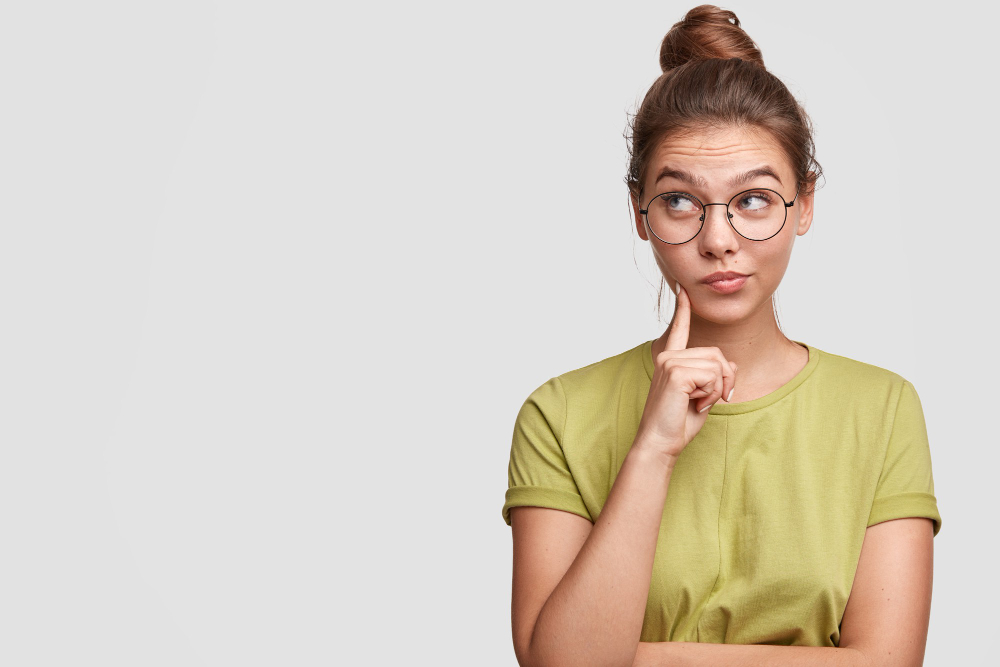
Why is the choice of PLC brand important in industrial automation?
Selecting the right PLC brand is crucial for ensuring the success and efficiency of industrial automation processes. Here’s why the choice matters:
- Compatibility: Different PLC brands may have varying communication protocols. Choosing a brand that aligns with existing systems ensures seamless integration.
- Application-specific Features: Each brand may offer unique features tailored to specific applications. Understanding the requirements of the automation task helps in selecting the most suitable PLC.
- Scalability: The scalability of a PLC system is vital for accommodating future expansions or modifications in the industrial setup. Opting for a brand with a scalable range of PLCs is advantageous.
- Support and Maintenance: The availability of technical support and ease of maintenance are crucial factors. Opting for a reputable brand often means access to reliable support services and readily available spare parts.
- Training and Resources: Learning resources, training programs, and documentation provided by the PLC brand can significantly impact the ease with which engineers and technicians adapt to the system.
In conclusion, the choice of a PLC brand should be a well-informed decision, considering factors such as compatibility, features, scalability, support, and training resources. Each brand has its strengths, and the selection should align with the specific needs of the industrial automation project.
What is the best answer to “What is PLC”?
The best answer to this question is a concise yet informative explanation of a PLC’s purpose and functionality in industrial automation. It’s about emphasizing how PLCs serve as the brains behind automated processes, making operations more efficient and responsive.
Why do we need PLC?
PLCs are essential because they provide a reliable and flexible means of controlling complex industrial processes. They improve efficiency, reduce manual intervention, and enhance overall system reliability, ensuring smooth and precise operations.
How to answer PLC interview questions?
To answer PLC interview questions effectively, it’s crucial to have a solid understanding of PLC basics, programming concepts, and practical applications. Emphasizing hands-on experience and problem-solving skills can also set you apart in an interview.
What is PLC and what example?
An example of a PLC application could be in a manufacturing plant where a PLC controls the sequence of operations on a production line. It reads input signals from sensors, processes the information, and triggers output signals to control machinery and maintain the desired production flow.
What is the difference between PLC and SCADA?
While PLCs focus on the control of processes, Supervisory Control and Data Acquisition (SCADA) systems are responsible for monitoring, gathering, and processing real-time data. PLCs and SCADA often work together, with PLCs managing the control aspects and SCADA overseeing the overall system.
Should I learn SCADA or PLC?
The decision to learn SCADA or PLC depends on your career goals. If you’re interested in hands-on control and automation, focusing on PLC is beneficial. However, a combination of both PLC and SCADA skills can open up broader opportunities in the field of industrial automation.
Can we use SCADA without PLC?
While SCADA systems can operate independently, they are often more effective when integrated with PLCs. PLCs handle the control logic, and SCADA provides the interface for monitoring and data visualization. Together, they create a comprehensive solution for industrial automation.
Is PLC more powerful than SCADA?
PLCs and SCADA serve different purposes, and comparing their power isn’t straightforward. PLCs excel in control and automation, whereas SCADA excels in data acquisition and visualization. The combination of both technologies is often more powerful in creating a robust industrial automation system.
What is SCADA used for?
SCADA systems are used for real-time monitoring, data acquisition, and control of industrial processes. They enable operators to visualize, analyze, and respond to the data generated by various sensors and devices in an industrial environment.
What is SCADA’s full form?
SCADA stands for Supervisory Control and Data Acquisition.
What is HMI and SCADA?
Human-machine interface (HMI) and SCADA are complementary technologies. HMI provides a user interface for operators to interact with the system, while SCADA extends this functionality by offering broader data visualization, analysis, and control capabilities.
What is an RTU in SCADA?
An RTU, or Remote Terminal Unit, is a device in SCADA systems that interfaces with sensors and equipment in remote locations. It collects data and communicates it to the central SCADA system for monitoring and control.
What does HMI stand for?
HMI stands for Human-Machine Interface.
Can HMI work without SCADA?
Yes, HMI can work independently without SCADA. While SCADA provides additional features for data analysis and system control, an HMI can function as a standalone interface for monitoring and interacting with industrial processes.
Can we connect PLC to SCADA?
Yes, PLCs and SCADA systems are often connected in industrial automation setups. PLCs handle the control logic and process data, while SCADA provides a centralized interface for monitoring, data visualization, and control.
What is the difference between SCADA and DCS?
SCADA and Distributed Control Systems (DCS) both manage industrial processes, but they differ in their architecture and scope. SCADA is typically used for monitoring and control, while DCS integrates control functions for a specific process in a centralized manner.
Can I use a PC as an HMI?
Yes, a PC can be used as an HMI. Software applications can turn a standard PC into a Human-Machine Interface, providing operators with a graphical interface to monitor and control industrial processes.
Conclusion:
In conclusion, understanding the basics of PLCs and related technologies like SCADA and HMI is crucial in the world of industrial automation. Whether you’re a novice exploring the field or an experienced professional seeking to enhance your skills, a solid foundation in PLC programming and related technologies opens up a world of opportunities. Consider joining a reputable institution like IIPD Global, which offers comprehensive PLC programming courses to kickstart or advance your career in industrial automation.
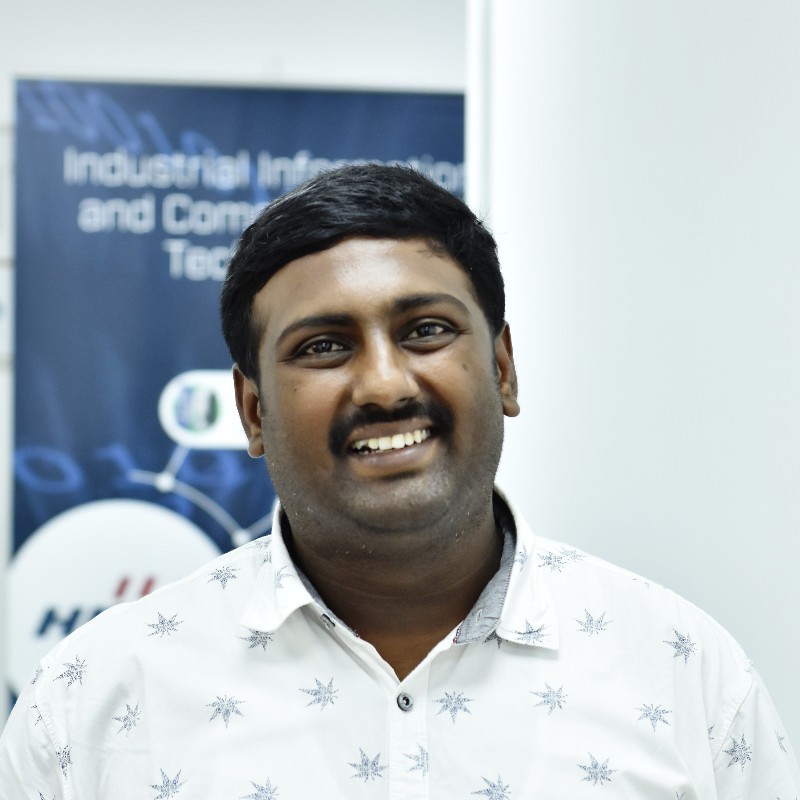
Senior Tech Manager at IIPD Global, weaving magic in Industrial, Building, and home Automation. KNX Tutor on a mission! Embracing Industry 4.0 and proudly shaping the tech landscape. Certified by CertNexus to ignite minds!