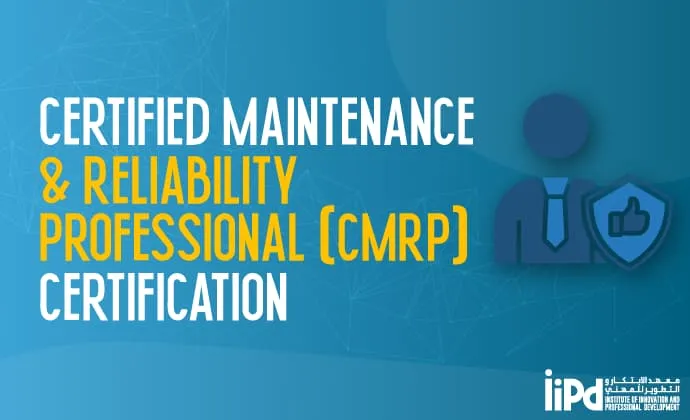
Course Details
An interactive training course covering Maintenance and Reliability best practices as defined by the Society for Maintenance and Reliability Professionals (SMRP) Body of Knowledge (BOK).
This course will enable participants to develop a strategy for outstanding maintenance and reliability performance, tools to improve reliability at the equipment level, and insight into the latest planning, scheduling, and control practices.
The Certified Maintenance and Reliability Professional standard is the leading accreditation for modern maintenance and reliability professionals. This top-tier qualification was established to set a consistent, recognized standard in the industry. It is the only certification accredited by the American National Standards Institute (ANSI). It follows the global standards of the Organization for Standards (ISO) for its accreditation process. Participants who pass the exam can use the designation 'CMRP.'
Known Best Practices will be explained, and demonstrated, and attendees will work on real-world issues in each functional area in maintenance and reliability.
The course will explain the concepts, tools, and processes of each element of the five pillars according to the body of knowledge guide.
Course Details
Course : | Certified Maintenance & Reliability Professional (CMRP) Certification |
Duration: | 5 days |
Language: | English |
Location: | Dubai, Riyadh, Dammam, Doha |
Course Objectives
This program aims to equip participants with current best practices and prepare them for the Certified Maintenance and Reliability Professional (CMRP) Exams.
- Learn how the SMRP Body of Knowledge can be applied to optimize asset reliability and maintainability.
- Identify how to use SMRP Metrics with their definitions and why this is critical to optimizing reliability.
- Create a Vision, Mission, and Guiding Principles for your Maintenance Organization
- Define Known Maintenance and Reliability Best Practices
- How to develop a plan to implement Maintenance and Reliability Best Practices
- Develop Maintenance-leading and Lagging KPIs for an Organization
- The most effective approach and process to Maintenance Planning and Scheduling
- Develop a PM Procedure
- Define failure modes for Specific Components and Assets
- Identify the difference between Reactive vs. Proactive Maintenance Attributes
- How to use SMRP Metrics to develop an organization into a more proactive state
- How the SMRP Body of Knowledge is mapped to SMRP Metrics, and why
- Benefits of Becoming a Member of SMRP
- How to create a Maintenance Strategy (PM/PdM)
- How to Manage Change
- Failure Reporting, Analysis, and Corrective Action System (FRACAS)
Upon successful completion of this course, participants will have:
- Clearer direction for career development and education
- Improved visibility and recognition within your current organization
- Develop effective methodologies to improve Manufacturing Process Reliability
- Describe the key aspects of improving reliability at the equipment level
- Utilize leadership skills to achieve maintenance and reliability excellence
- Demonstrate best practices in Work Management, including the principles of managing workflow and planning and scheduling
- Assists in job promotion
- Greater job effectiveness
- Fewer frustrations with gaps in knowledge
- Improved ability to differentiate between candidates in the hiring and promotion process
Top 10 Benefits of Attendance
- "Known Best Practices in Maintenance and Reliability" from around the world.
- Maintenance Work Process Management
- Barriers and Solutions to Effective Work Force Management
- Operator Driven Reliability. Importance of 5S and Total Productive Maintenance
- Maintenance Strategy Development & Reliability Centered Maintenance
- Types of Predictive maintenance tools and their uses.
- Designing Reliability Asset Life Cycle Cost.
- Inventory Management, and Economic Order Quantity (EOQ)
- Maintenance and reliability tools such as RCA, FMEA, and OEE.
- Leading & Lagging KPIs, Benchmarking for Proactive Maintenance
Who Should Attend?
A Certified Maintenance and Reliability Professional (CMRP) is ideal for
- Maintenance and Reliability Professionals at all levels.
- Experienced supervisors, planners, project engineers, operations managers, functional specialists, and those seeking to achieve the CMRP designation will also benefit from this course.
- Production/Operations Professionals
- Senior Managers
Training Methodology
This is an interactive course. There are open question and answer sessions, regular group exercises and activities, videos, case studies, and presentations on best practices and the fundamentals of reliability improvement. Participants will be trained on the CMRP real exam questions with many examples.
Course Outline
Below is the course content, which includes a detailed outline of topics and materials covered in the course. Explore and enhance your knowledge!
1.0 Business and Management
This subject area describes the skills used to translate an organization’s business goals into appropriate maintenance and reliability goals that support and contribute to the organization’s business results.
1.1 Create Strategic direction and plan for M&R operations
- Provide vision and direction
- Provide clear and measurable goals
1.2 Administer Strategic plan
- Develop support
- Obtain approval and resources
- Implement plans
1.3 Measure Performance
- Select key performance indicators
- Track and report
1.4 Manage organizational plan
- Develop change management process
- Communicate benefits
1.5 Communicate with stakeholders
- Provide management reports
- Inform staff
- Coordinate with operations
1.6 Manage environmental-health-safety risk
- Support community EHS goals
- Support security goals
- Conform to applicable regulations
- Provide EHS training
2.0 Manufacturing Process Reliability
This subject area relates maintenance and reliability activities to the manufacturing process of the organization to ensure that maintenance and reliability activities improve the manufacturing process.
2.1 Understand the applicable processes
- Document process flow
- Understand process parameters
- Understand quality specifications
2.2 Apply process improvement techniques
- Identify production losses
- Establish a continuous improvement process
2.3 Manage effects of change to processes and equipment
- Establish change protocol
- Update documentation
- Update procedures
2.4 Maintain processes per applicable standards and regulations
- Understand industry standards
- Understand regulatory requirements
- Ensure compliance
3.0 Equipment Reliability
This subject area describes two kinds of activities that apply to the equipment and processes for which the maintenance and reliability professional is accountable. First, are those activities used to assess the current capabilities of the equipment and processes in terms of their reliability, availability, maintainability, and criticality. Second are the activities used to select and apply the most appropriate maintenance practices, so that the equipment and processes continue to deliver their intended capabilities most safely and cost-effectively.
3.1 Determine equipment reliability expectations
- Identify reliability goals
- Identify process expectations
3.2 Evaluate equipment reliability and identify improvement opportunities
- Measure and track performance
- Determine best-demonstrated performance
- Analyze gaps
3.3 Establish a strategic plan to ensure the reliability of existing equipment
- Identify appropriate analysis techniques
- Develop maintenance strategy and tactics
3.4 Establish a strategic plan to ensure the reliability of new equipment
- Establish reliability specifications
- Establish acceptance criteria
- Obtain complete documentation
3.5 Cost-justify selected plans for implementation
- Conduct cost-benefit analysis
- Communicate benefits
- Obtain approval
3.6 Implement selected plans to ensure equipment reliability
- Apply reliability strategies
- Establish organization structure
- Provide resources
3.7 Review the reliability of equipment and adjust the reliability strategy
- Assess key performance indicators
- Analysis deviations
- Identify relevant best practices
- Implement continuous improvement
4.0 Organization & Leadership
This subject area describes processes for assuring that the maintenance and reliability staff is the most qualified and best assigned to achieve the maintenance and reliability organization goals.
4.1 Determine organizational requirements
- Review strategic plan
- Determine required skills
- Determine required staffing levels
4.2 Analyze organizational capability
- Inventory staff skills
- Determine performance gaps
4.3 Develop the organization structure
- Establish reporting channels
- Determine roles
- Determine responsibilities
- Manage reorganization
4.4 Develop personnel
- Provide training
- Obtain needed expertise
- Delineate career paths
4.5 Lead and manage people
- Develop leadership skills
- Assess performance
- Promote a cooperative work
environment - Facilitate communication
5.0 Work Management
This subject area focuses on the skills used to get the maintenance and reliability work done. It includes planning and scheduling activities, quality assurance of maintenance activities, stores, and inventory management.
5.1 Identify, validate, and approve work
- Establish work identification processes
- Select and approve viable work
5.2 Prioritize work
- Develop a formal prioritizing system
- Implement formal prioritizing system
5.3 Plan work
- Develop job package
- Including scope and procedures
- Including materials and tools
- Including testing
5.4 Schedule work
- Develop scheduling process
- Produce work schedule
- Balance resources
- Monitor backlog
- Manage break-in work
- Coordinate equipment access
5.5 Execute work
- Manage labor
- Manage material and services
- Control Productivity
- Ensure EHS compliance
5.6 Document work
- Create post-work document process
- Record failure events and failure modes
5.7 Analyze work and follow-up
- Compare actual work with plan
- Identify variances
5.8 Measure work management performance
- Establish performance indicators
- Report schedule compliance and
rework
5.9 Plan and execute projects
- Define scope
- Estimate project and life cycle costs
- Apply critical path methods
- Track progress
- Coordinate staffing
5.10 Use information technologies Effectively
- Leverage capabilities of data historian
- Process control systems
- Condition monitoring software
- EAM,CMMS systems functionality
5.11 Manage resources and materials
- Control materials inventory
- Manage spares and equipment
- Establish MRO procurement process
- Manage contractors
Separate Session:
- CMRP Certification Exam Question and Answer Examples
Enroll now in the Advanced Reliability Centered Maintenance course by IIPD Global and embark on a transformative learning journey that will unlock new opportunities and propel your career to new heights. We look forward to welcoming you and supporting your growth in the exciting field of maintenance management.